top of page
Jacob Klein
Welcome to my portfolio! Here you'll find a collection of my engineering projects, showcasing my work in design, analysis, and innovation across aerospace and mechanical systems. Feel free to explore each project to learn more about my technical skills, problem-solving approach, and hands-on experience.
My Portfolio
Here you’ll find different areas of my work. Explore my projects to learn more about what I do.
For access to the PDF files, please email me at jacobklein421@gmail.com
CubeSat Design

Clairvoyance is a dual-CubeSat mission designed to deliver scientific payloads to the Earth-Sun Lagrange Point 5 (L5) to monitor space weather and survey for asteroids over a one-year operational period. The mission consists of two 12U CubeSats: the Servicer, which houses the primary propulsion and docking systems, and the Client, which carries instruments including a coronagraph and an infrared camera. Launched via SpaceX Falcon 9 and boosted with the Impulse Helios kick stage, the spacecraft will perform a multi-phase heliocentric transfer, autonomous docking in transit, and station-keeping at L5. Despite propulsion and communication challenges, the system is optimized for mass, energy efficiency, and mission longevity, with an estimated mission duration of over three years.
RC Plane Design
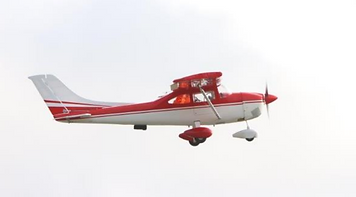
The aircraft includes onboard avionics with a Pixhawk Mini, real-time telemetry, and autonomous waypoint navigation. The wing design employs a NACA 2412 airfoil and was optimized through AVL and MATLAB simulations to improve lift-to-drag ratio, spanwise load distribution, and dynamic stability. The final configuration demonstrates favorable static and dynamic stability characteristics, confirmed through computed derivatives and eigenmode analysis. It satisfies regulations for both aerodynamic stability and structural integrity, with all subsystems co-designed to ensure smooth airflow, structural robustness, and precise control in dynamic flight scenarios.
Water Cooling System

This water cooling system was developed to prevent thermal failure during combustion of isopropyl alcohol and nitrous oxide in the Sparrow V1 rocket engine. The system delivers a pressurant-fed water flow of up to 1 kg/s at 100 psi to the engine’s cooling manifold. It integrates a keg-based water reservoir, flexible tubing for engine gimbaling, and compression fittings for a secure nozzle connection. Key design decisions included using filtered water to protect small-diameter cooling lines and selecting compressed air over nitrogen for cost and handling efficiency. The system was optimized for trailer integration, rapid deployment, and safe operation under high pressures.
eVTOL Design

GatorFly is a fully electric vertical takeoff and landing (eVTOL) aircraft designed by the VTOL team at the University of Florida for the 39th Annual Vertical Flight Society Design Competition. It accommodates both able-bodied and disabled passengers with a configurable cabin layout, rear-ramp accessibility, and onboard medical equipment storage. The final configuration combines a tilt-wing airframe with four EMRAX 348 motors with two tilting in front and two fixed at the rear for safe, efficient transition between vertical and horizontal flight. The aircraft features a NACA 2412 wing for aerodynamic efficiency, a carbon fiber skin with aluminum 7075 internal structure, and skid landing gear for simplicity and stability.
Mechanical Manipulator

This project involved the design, fabrication, and testing of a remote-controlled robot capable of manipulating and stacking wooden blocks during a timed competition. The robot featured a custom-built arm with a hinged gripper for precision block handling, a motorized manipulator assembly, and a folded plow for efficient block gathering. Key improvements during development included the addition of rubber grips to the manipulator for increased friction and a redesigned plow with spot-welded tabs to simplify manufacturing. The final robot performed successfully in competition, achieving full points while demonstrating robust control, structural reliability, and effective task execution.
Finite Element Analysis

I completed two comprehensive finite element analysis projects focused on structural optimization. The first project involved designing a lightweight aluminum bicycle frame using beam elements in Abaqus, applying iterative fully stressed design and buckling analysis to meet safety margins under vertical and horizontal loads. The second project centered on optimizing a torque-arm under combined loading. It included convergence and mesh refinement studies, element type comparisons, and a mass minimization process using 2D plane stress elements. Both projects emphasized simulation accuracy, material efficiency, and real-world structural performance through analytical and computational methods.
Wind Tunnel Lab

In Wind Tunnel Lab, I conducted a series of wind tunnel experiments focused on subsonic flow behavior, pressure distributions, and wake analysis around aerodynamic geometries. Initial labs involved calibrating wind tunnel equipment and mapping velocity profiles to observe boundary layer effects and incompressible flow behavior. I measured surface pressure distributions on a cylinder and a NACA 0012 airfoil to calculate lift, drag, and moment coefficients at various angles of attack, comparing experimental results with theoretical and XFOIL data. Using hot-wire anemometry, I captured wake turbulence and vortex shedding frequencies, performing FFT analysis to determine Strouhal numbers. Additional studies involved characterizing drag over a range of Reynolds numbers using a two-component dynamometer, and comparing the aerodynamic wake interactions of multi-cylinder configurations. The final project integrated these methods to evaluate the velocity profiles and shedding behavior of two- and three-cylinder assemblies, reinforcing key concepts in wake dynamics, flow separation, and experimental fluid mechanics.
Mechanics of Materials Lab

Throughout Mechanics of Materials Lab, I conducted multiple experiments focused on mechanical testing, instrumentation, and material characterization. I designed and calibrated a cantilever beam transducer using strain gauges and a Wheatstone bridge to measure applied force and strain. I also performed tensile and compressive testing of materials with stainless steel, nylon 6-6, carbon fiber, and plaster to generate stress-strain curves and extract mechanical properties such as yield strength and modulus of elasticity. Additional labs involved evaluating adhesive joint strength using double-lap shear testing and analyzing vibrations in beams using strain gauges and accelerometers with FFT to determine material stiffness. These projects emphasized hands-on data acquisition, signal processing, uncertainty analysis, and the integration of mechanical principles with sensor-based measurements.
Dynamics and Controls Lab

In Dynamics and Controls Lab, I developed and evaluated control systems for a motor-flywheel and rotational pendulum setup through experimental modeling and controller design. I derived transfer functions using both time-domain and frequency-domain methods, generating Bode plots and step responses to characterize system dynamics. I implemented and analyzed multiple control strategies including bang-bang, PID, full-state feedback using Ackerman’s method, and Linear Quadratic Regulator (LQR) to assess rise time, overshoot, and steady-state error. The final project involved optimizing PD and LQR controllers to minimize pendulum swing while tracking a square wave rotation on the platen, using state-space modeling and MATLAB-based simulation.
Thermal Sciences Lab

In Thermal Sciences Lab, I completed a series of experiments and a final design project focused on real-world thermal and fluid systems. I characterized head loss and friction factors in pipe networks, evaluated heat transfer efficiency and fouling in a double-pipe heat exchanger, and analyzed performance curves and energy efficiency of centrifugal fans with different impeller types. I also assessed cooling tower performance through psychrometric analysis of latent and sensible heat transfer under variable loads. The final project involved designing a hydraulic oil transport system, including pump sizing, head loss estimation, and valve selection, to meet precise flow and pressure requirements. Across all labs, I applied first-law energy balances, fluid mechanics, uncertainty analysis, and system-level engineering design.
Aerospace Structures

This project analyzed the structural safety and fatigue life of the Boeing 767-400ER wing-box using beam theory, fracture mechanics, and fatigue modeling. Key tasks included calculating shear force and bending moment distributions, determining stress concentrations at fastener holes, and assessing static failure using Tresca and Von Mises criteria. A fatigue life analysis predicted safe operation for over 95,000 load cycles, while crack growth analysis using the Paris model indicated 114,605 cycles to fracture from an initial flaw. The overall factor of safety was 1.70, but the presence of a root-section crack reduced it to 1.025, highlighting the importance of early crack detection and structural inspection.
Compressible Flow

This project involved a detailed preliminary design and performance analysis of a supersonic wind tunnel using isentropic flow theory and compressible flow principles. Calculations were performed to determine the nozzle throat size, stagnation pressures, mass flow rates, and required storage volumes for various test section dimensions (4x3, 6x6, and 12x12 in²), Mach numbers (1.5 to 5.0), and diffuser angles (3°–5°). The study also analyzed the impact of expansion assumptions (isentropic vs. isothermal) on reservoir sizing and calculated sidewall angles to maintain uniform Mach flow in the test section. Trends were visualized through graphs, and results confirmed that increased Mach numbers require higher stagnation pressures but smaller storage volumes, highlighting trade-offs in supersonic tunnel design.
bottom of page